SURVIVAL THROUGH QUALITY
PRODUCT CENTER
-
Pulse dust collector
-
Mine dust collector
-
Boiler dust collector
-
Metallurgical dust collector
-
Carbon plant dust collector
-
Chemical dust collector
-
Rubber dust collector
-
Woodworking dust collector
-
Single machine dust collector
-
Static electricity Dust collector
-
Cyclone dust collector
-
Wet dust collector
-
Filter cartridge dust collector
-
Insert valve (gate valve)
-
Ventilation butterfly valve (cold air valve)
-
Spiral conveyor (auger)
-
Scraper conveyor
-
Dust humidifier
-
Bucket elevator
-
Ash discharge valve
-
Material Handling Equipment
-
Wet scrubber
-
Dust collector
-
Dust removal filter bag
-
Dust removal bag cage
-
Polishing platform
-
Waste gas treatment equipment
-
Electric control cabinet
-
Fan
-
Smoke welding machine
-
Liquid level switch
-
Dust removal filter element
-
Aeration cushion
-
Sweeper
-
Dust suppression device
-
Solenoid valve
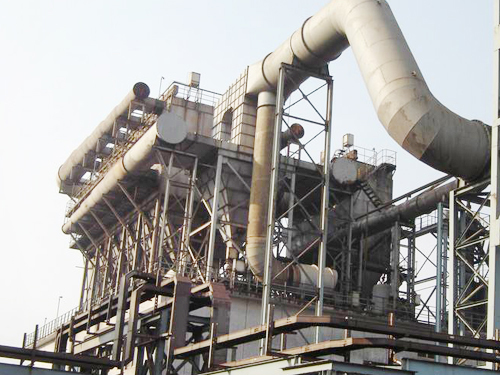
Coking furnace smoke and dust collector
According to the theory of electric field, positive ions are adsorbed on negatively charged corona and negative ions are adsorbed on positively charged precipitate in the smoke and dust collector of coke oven; All ionized positive and negative ions fill the entire space between corona and precipitation. When coal gas containing impurities such as tar droplets passes through this electric field, the impurities that adsorb negative ions and electrons move to the precipitate under the Coulomb force of the electric field, release the charged particles, and adsorb them onto the precipitate to achieve the purpose of purifying the gas, which is commonly known as the phenomenon of charging. When the amount of impurities adsorbed on the sediment increases beyond its adhesion, it will automatically flow downwards and be discharged from the bottom of the electric tar catcher. The net gas will leave the upper part of the electric tar catcher and enter the next process.
Treatment of Coking Oven Smoke and Dust Eliminators:
The coal material loaded into the carbonization chamber is entrained with a large amount of air. At the beginning of coal loading, the oxygen in the air and the fine coal particles entering the furnace burn to produce carbon black, forming black smoke. When coal is loaded into the furnace and comes into contact with the hot furnace wall, a large amount of carbon, sulfur, nitrogen elements and compounds are generated during heating, accompanied by water vapor and hydrocarbons. At this time, the flue gas becomes dark yellow. One part of it enters the coke oven gas collection pipe, while the other part overflows through the top exhaust hole and the gap between the furnace doors, accounting for about 60% of the total emissions of the coke oven.
In the process of coal loading, a large amount of substances such as coal powder, raw gas, sulfur and nitrogen oxides are discharged from the flue gas, including polycyclic aromatic hydrocarbons that pose a serious threat to human health, such as benzopyrene, 7,12-dimethylbenzoanthracene, 3-diananthrene, dibenzopyrene, and dibenzopyrene. If left untreated, it will cause serious pollution to the surrounding environment, worsen working conditions, and pose a great threat to the physical health of employees, violating environmental policies. Therefore, strong measures should be taken to strengthen the control of overflow smoke during coal loading.
According to statistics, during the coal loading process of coke ovens, the pollutant emissions per ton of coal fed into the furnace are about 2.37kg, among which the main pollutants are solid particulate matter (TSP), benzo pyrene (Bap), benzene soluble organic matter (BSO), sulfur dioxide (S02), etc. The BSO emissions are 0. 499kg/t coal, with a Bap emission of 0.000908kg/t coal, all substances such as Bap exist as carriers of TSP. Therefore, the collection and treatment of pollutants on TSP are the key to controlling coke oven pollution.