SURVIVAL THROUGH QUALITY
PRODUCT CENTER
-
Pulse dust collector
-
Mine dust collector
-
Boiler dust collector
-
Metallurgical dust collector
-
Carbon plant dust collector
-
Chemical dust collector
-
Rubber dust collector
-
Woodworking dust collector
-
Single machine dust collector
-
Static electricity Dust collector
-
Cyclone dust collector
-
Wet dust collector
-
Filter cartridge dust collector
-
Insert valve (gate valve)
-
Ventilation butterfly valve (cold air valve)
-
Spiral conveyor (auger)
-
Scraper conveyor
-
Dust humidifier
-
Bucket elevator
-
Ash discharge valve
-
Material Handling Equipment
-
Wet scrubber
-
Dust collector
-
Dust removal filter bag
-
Dust removal bag cage
-
Polishing platform
-
Waste gas treatment equipment
-
Electric control cabinet
-
Fan
-
Smoke welding machine
-
Liquid level switch
-
Dust removal filter element
-
Aeration cushion
-
Sweeper
-
Dust suppression device
-
Solenoid valve
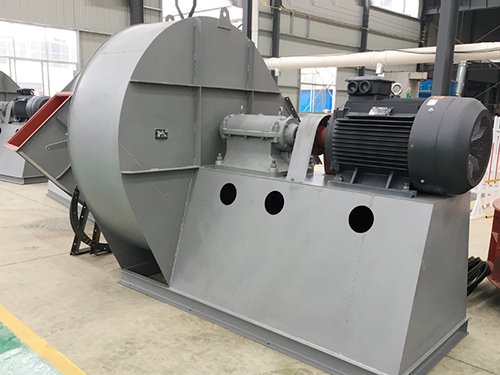
Induced draft fan
Induced draft fan is a device that generates negative pressure through the rotation of the impeller, and then extracts air from the system (equipment). It is generally installed at the tail end of the boiler to extract hot flue gas from the furnace.
In daily life, ventilation fans are usually divided into induced draft fans (for negative pressure use) and blowers (for positive pressure use) according to their different usage methods. Induced draft fans are widely used for ventilation, dust removal, and cooling in factories, mines, tunnels, cooling towers, vehicles, ships, and buildings; Ventilation and induced draft of boilers and industrial furnaces; Cooling and ventilation in air conditioning equipment and household appliances; Drying and selection of grains; Wind tunnel sources and inflation and propulsion of hovercraft. The working principle of the induced draft fan is basically the same as that of a turbine compressor, but due to the low gas flow rate and little pressure change, it is generally not necessary to consider the change in gas specific volume, that is, to treat the gas as an incompressible fluid.
Wear resistant ceramic fans and impellers refer to the main flow components in the fan, including the fan impeller, volute, inlet and outlet, damper, and pipeline system, which are heavily worn parts. A layer of wear-resistant ceramic is composite on them. At the same time, using the three source flow theory, the shape and shell of the impeller are optimized and designed to form a high wear-resistant or new functional fan equipment. The wear-resistant fan adopts new fan design technology, ceramic metal composite manufacturing technology, polymer composite ceramic technology, vacuum bonding technology, cold welding and gas protection welding technology, as well as non-destructive testing technology. The surface layer makes the product have the most advanced technological level at present.
Performance characteristics:
Due to the hardness HRA ≥ 86 (toughened alumina composite material) of the composite ceramic layer on the working surface of the fan impeller, secondary sintering of silicon nitride toughened ceramics or zirconia toughened alumina ceramics can be used in severely worn areas, with a maximum of HRA94 or above. Its particle erosion wear resistance can be at least 5 times higher than conventional treatment methods such as ordinary tungsten carbide overlay welding, spray welding, and alloy powder block welding, and more than 100 times higher than the base 16Mn steel; The ceramic plate with a thickness of 1.5mm has been in use for five years, and the average wear is less than 0.2mm.
Application scope:
The wear-resistant fan impeller has a wide range of applications, mainly determined by the operating temperature of the fan, and is not affected by the wear medium. According to different working temperatures, the usage range of wear-resistant ceramic fans is divided into three areas, namely:
Normal temperature working range: Temperature below 120 degrees Celsius, using conventional polymer composite technology
Medium temperature working range: Temperature between 120-180 degrees Celsius, using high-temperature resistant polymers and cold welding technology
High temperature working range: Temperature between 180~380 degrees Celsius, using ceramic metal welding+high-temperature resistant polymer material technology.