SURVIVAL THROUGH QUALITY
PRODUCT CENTER
-
Pulse dust collector
-
Mine dust collector
-
Boiler dust collector
-
Metallurgical dust collector
-
Carbon plant dust collector
-
Chemical dust collector
-
Rubber dust collector
-
Woodworking dust collector
-
Single machine dust collector
-
Static electricity Dust collector
-
Cyclone dust collector
-
Wet dust collector
-
Filter cartridge dust collector
-
Insert valve (gate valve)
-
Ventilation butterfly valve (cold air valve)
-
Spiral conveyor (auger)
-
Scraper conveyor
-
Dust humidifier
-
Bucket elevator
-
Ash discharge valve
-
Material Handling Equipment
-
Wet scrubber
-
Dust collector
-
Dust removal filter bag
-
Dust removal bag cage
-
Polishing platform
-
Waste gas treatment equipment
-
Electric control cabinet
-
Fan
-
Smoke welding machine
-
Liquid level switch
-
Dust removal filter element
-
Aeration cushion
-
Sweeper
-
Dust suppression device
-
Solenoid valve
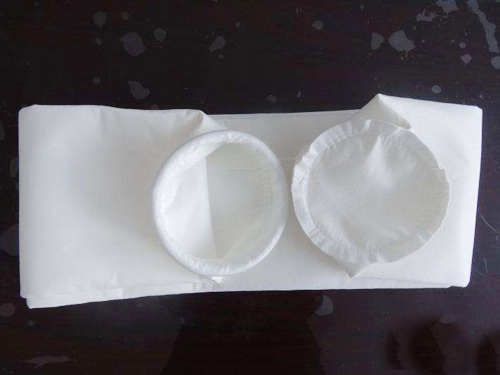
Water repellent, oil proof, and dust removal cloth bag
The dust removal bag uses reactive fluoride additives to post-treat various filter materials such as polyester, polypropylene, needle punched felt, and aramid needle punched felt to produce products. The grade test of the dust removal bag meets the standard, and it does not affect the appearance style and internal indicators of the original needle punched felt bag.
The production process of dust removal bags is as follows:
Fiber loosening - combing - laying net - pre piercing - main piercing - felting - singeing - calendering - impregnation - PTFE (agent) drying - shaping - rolling - coiling.
The filter bag made by treating the filter cloth with polyester needle punched felt dust removal bag is applied in situations with high moisture content. Compared with ordinary filter bags, needle punched felt extends the cleaning cycle and service life of the filter bag because the filter material is not easy to block and paste the bag. The gas flow rate also increases, which can save energy consumption and maintenance costs, while also increasing production.
Dust removal bags are mainly used in industries such as cement and building materials, steel, non-ferrous smelting, coking and refractory, chemical industry, mechanical casting, crushing and polishing, food, medicine, and mill matching.
The working mechanism of dust removal bags:
Using reactive fluoride additives to prepare a mixed working solution for impregnating filter media, the working solution reacts with certain functional groups in the fiber macromolecular structure of the filter media, forming macromolecular chains, changing the affinity between fibers and water and oil, reducing the surface tension of the filter media to less than the surface tension of water and oil, in order to achieve the goal.
Advantages of dust removal bags:
1. Surface incomplete filtration: Typically, industrial filter materials are used for deep filtration. It relies on establishing a dust layer on the surface of the filter material to achieve filtration. Long filtration time, high resistance, low efficiency, poor interception, high filtration and backflushing pressure, frequent ash cleaning, high energy consumption, short service life, and large equipment footprint. When using membrane covered dust removal filter bag filter material, dust cannot penetrate into the filter material and is filtered on the surface. Both coarse and fine dust settle on the surface of the filter material, which is intercepted by the pore size of the membrane itself. There is no initial filtration period, and it is filtered from the beginning to the near future.
2. When using dust removal cloth bag filter material, dust cannot penetrate the filter material and is filtered on the surface. Both coarse and fine dust settle on the surface of the filter material, which is intercepted by the pore size of the membrane itself. There is no initial filtration period, and it is filtered from the beginning to the near future.
3. Easy to clean: The operating pressure loss of any filter material directly depends on the amount of dust remaining or retained on the surface of the filter material after cleaning, the length of cleaning time, and has excellent cleaning characteristics. Each time the dust layer is removed, the inside of the filter material will not cause blockage, and the porosity and mass density will not be changed. It can frequently maintain low pressure loss work.
4. Long lifespan: No matter what cleaning mechanism is used, the membrane filter material can play a common and excellent role. It is a filter material that utilizes the design function of the dust collector to filter. Therefore, the cost is low. Membrane filter material is a strong and soft fiber structure that is compounded with a strong substrate. So it has sufficient mechanical strength, combined with some deashing properties, which reduces the cleaning strength. Under low and stable pressure loss, it can be used for a long time and extend the service life of the filter bag.
5. Low pressure, continuous flux operation: Traditional deep filtration media, once put into use, penetrate the dust and establish a dust layer, resulting in a decrease in breathability. When filtering, the accumulated dust inside causes blockage, which increases the resistance of the dust removal equipment. The membrane filter material has a micro pore size and its lower viscosity, which makes the dust penetration rate close to zero. When put into use, it provides filtration efficiency. When the filtered material deposited on the surface of the membrane filter material reaches its thickness, it will automatically fall off and be easy to clean, keeping the filtration pressure at a low level and the air flow rate at a low level, allowing for continuous operation.
6. Low pressure, high-throughput continuous operation. Traditional deep filtration filter media.
7. Dust removal bags are easy to clean and have a long service life.
Filter material name | Polyester needle punched felt filter material | |
material quality | Polyester fiber | |
Gram weight (g/m2) | 500 | |
Thickness (mm) | 1.80 | |
Breathability (m3/min) | 12 | |
Breaking strength (N/5 x 20cm) | Meridian | >800 |
Latitudinal direction | >1250 | |
Breaking elongation (%) | Meridian | <35 |
Latitudinal direction | <50 | |
Continuous working temperature (℃) | ≤130 | |
Short term working temperature (℃) | 150 | |
Grade (water temperature 27 ℃, relative humidity 20%) | Level 5 AATCC100 | |
Acid resistance | good | |
Alkali resistance | good | |
performance | excellent | |
Hydrolysis stability | good | |
surface treatment | Treatment (Teflon coating) |