SURVIVAL THROUGH QUALITY
PRODUCT CENTER
-
Pulse dust collector
-
Mine dust collector
-
Boiler dust collector
-
Metallurgical dust collector
-
Carbon plant dust collector
-
Chemical dust collector
-
Rubber dust collector
-
Woodworking dust collector
-
Single machine dust collector
-
Static electricity Dust collector
-
Cyclone dust collector
-
Wet dust collector
-
Filter cartridge dust collector
-
Insert valve (gate valve)
-
Ventilation butterfly valve (cold air valve)
-
Spiral conveyor (auger)
-
Scraper conveyor
-
Dust humidifier
-
Bucket elevator
-
Ash discharge valve
-
Material Handling Equipment
-
Wet scrubber
-
Dust collector
-
Dust removal filter bag
-
Dust removal bag cage
-
Polishing platform
-
Waste gas treatment equipment
-
Electric control cabinet
-
Fan
-
Smoke welding machine
-
Liquid level switch
-
Dust removal filter element
-
Aeration cushion
-
Sweeper
-
Dust suppression device
-
Solenoid valve
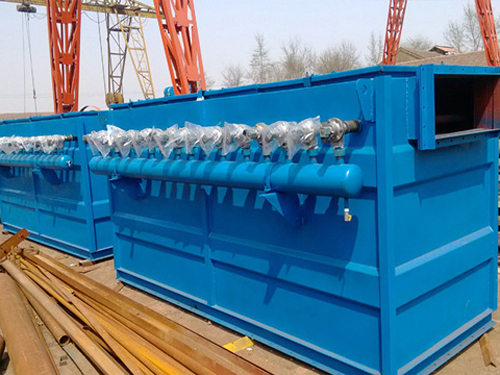
XMC pulse single machine dust collector
The XMC pulse single machine dust collector is a technology that uses high-pressure (0.5-0.4MPa) high flow pulse valves to spray and clean the dust one by one through the filter bags. Can collect the above dust from a large amount of dust gas (1300g/m3). At present, under the new environmental protection standards, it is not only widely used for dust control in cement plants, but also widely used for deep processing of non-metallic mineral fine powder. It has good application prospects in industries such as power, chemical, metallurgy, and steel.
The XMC pulse single machine dust collector can be used in the dust and smoke collection system of asphalt mixing plants, such as crushing, grinding, drying machines, furnaces, etc. The material of the filter bag of the dust collector is generally polyester needle punched felt, which allows continuous use at a temperature of ≤ 120 ℃. If the filter bag is made of Mettas high-temperature needle punched felt, its allowable use temperature can reach 204 ℃.
The XMC pulse single machine dust collector can be combined with multiple different specifications of dust collectors according to different specifications of solenoid valves. This series of dust collectors can operate under negative pressure or positive pressure, with no changes in its main structure. The dust collection efficiency reaches over 90%, and the dust concentration of the purified gas is less than 100mg/m3. If used in cold areas or when the smoke is below zero point, insulation heating devices need to be added, and the shell also needs to be subjected to phase strain.
XMC pulse single machine dust collector structure:
1) Box: including bag room, pre dust collection room, air purification room, porous plate, filter bag, and filter bag skeleton. The box design has a pressure resistance of 9000Pa.
2) Spray system: including main air pipe, spray pipe, pulse valve, and control instrument.
3) There are two forms of ash hopper and ash discharge part: one is that the ash hopper is directly connected to the ash discharge valve, and the other is that the ash hopper is connected to the ash discharge valve through conveying equipment (such as screw conveyor).
Working principle of XMC pulse single machine dust collector:
When the dusty gas enters the dust collector through the air inlet, it first touches the inclined plate and baffle in the middle of the air inlet and outlet, and the airflow turns to flow into the ash hopper. At the same time, the airflow speed slows down, and due to the inertia effect, the coarse dust particles in the gas directly flow into the ash hopper. It serves as a pre dust collector, where the airflow entering the ash hopper is then folded upwards and captured on the outer surface of the filter bag through the filter bag with a metal skeleton inside. The purified gas enters the upper cleaning room of the filter bag room and is collected at the air outlet for sequential circulation to complete the dust removal purpose.
Precautions for the operation of XMC pulse single machine dust collector:
(1) When starting the XMC pulse single machine dust collector, the compressed air should be connected to the air storage tank, the control power should be connected, and the ash discharge device should be started. If there are other equipment in the system, the downstream equipment should be started first.
(2) When the XMC pulse single machine dust collector is shut down, it is not necessary to cut off the compressed air source, especially when the fan is working, to provide compressed air to the lifting valve cylinder to lift the valve in an open state.
(3) The oil-water separator in the gas storage tank and gas source triple unit should be discharged once per shift, and the oil-water separator in the industrial dust collector should be cleaned every 3-6 months. The oil mist collector should be regularly checked for oil storage and refilled in a timely manner.
(4) If the XMC pulse single machine dust collector malfunctions, it should be promptly eliminated. If there are impurities or moisture inside, it should be cleaned. If the diaphragm is damaged, it should be cleanedReplace in a timely manner.
(5) When the XMC pulse single machine dust collector is operating normally, the ash discharge device cannot stop working. Otherwise, the ash hopper will quickly accumulate dust and overflow into the bag room, forcing the industrial dust collector to stop working.
(6) The XMC pulse single machine dust collector regularly measures process parameters, such as smoke volume, temperature, concentration, etc. If abnormalities are found, the cause should be identified and dealt with in a timely manner.
(7) Management personnel should be familiar with the principles, performance, and usage conditions of industrial dust collectors, and master the methods of adjustment and maintenance.
(8) When shutting down, after the process system stops, the industrial dust collector and exhaust fan should continue to work for a period of time to remove moisture and dust from the dust removal equipment. It should be noted that when the industrial dust collector stops working, it should be repeatedly cleaned (manually) to remove dust from the dust removal filter bag and prevent it from being affected by moisture and sticking to the bag.
(9) The mechanical moving parts of the XMC pulse single machine dust collector, such as the reducer and ash conveying device, should be lubricated and replaced according to regulations. Any abnormal phenomena should be promptly eliminated.
(10) The XMC pulse single machine dust collector uses a timed dust cleaning controller, and the accuracy of the dust cleaning cycle should be regularly measured. Otherwise, adjustments should be made. When using a fixed resistance pulse controller, the working condition of the pressure switch should be regularly checked, the pressure measuring port should be checked for blockages, and cleaned.